Nickel-based alloy
Nickel 718
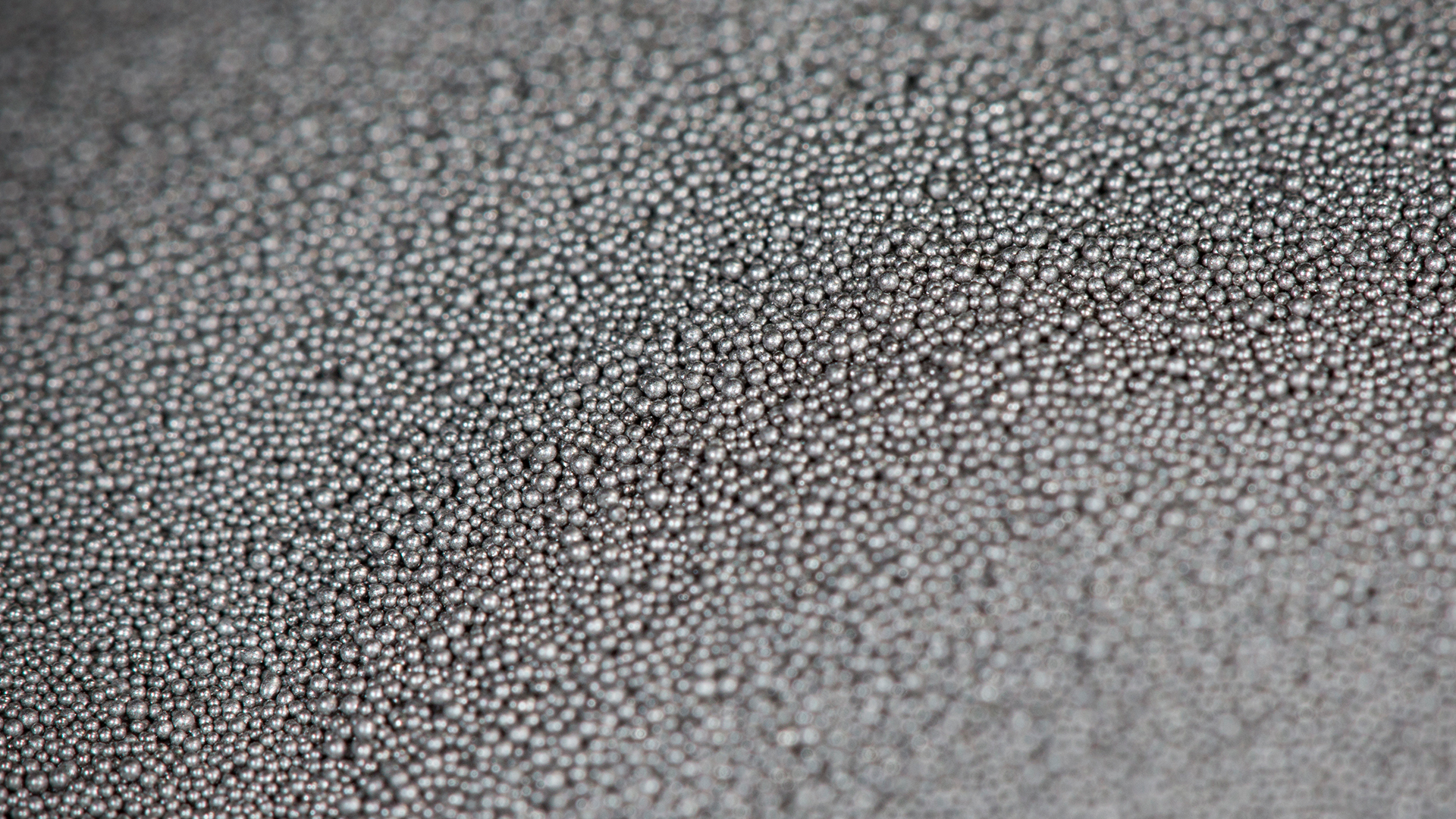
Nickel-based alloy
Nickel 718
Nickel chromium superalloys are often used in high-stress, high-temperature aeronautical, petrochemical and auto racing environments. The excellent high temperature strength and creep resistance derive from precipitation hardening of finely dispersed precipitates. Nickel Alloy 718 is a metal that is also highly resistant to the corrosive effects of hydrochloric acid and sulfuric acid. The favorable weldability of Nickel Alloy 718 makes this alloy suitable for additive manufacturing as well. Typical applications are high-quality components designed for thermally challenging environments such as rocket engines, gas-turbine hot sections, and heat exchangers.
Powder chemical composition may comply with standards: ASTM B637, ASTM F3055, AMS5596, AMS5662, AMS5664, AMS7006 or equivalent standard
Powder chemical composition may comply with standards: ASTM B637, ASTM F3055, AMS5596, AMS5662, AMS5664, AMS7006 or equivalent standard
Particle size distribution
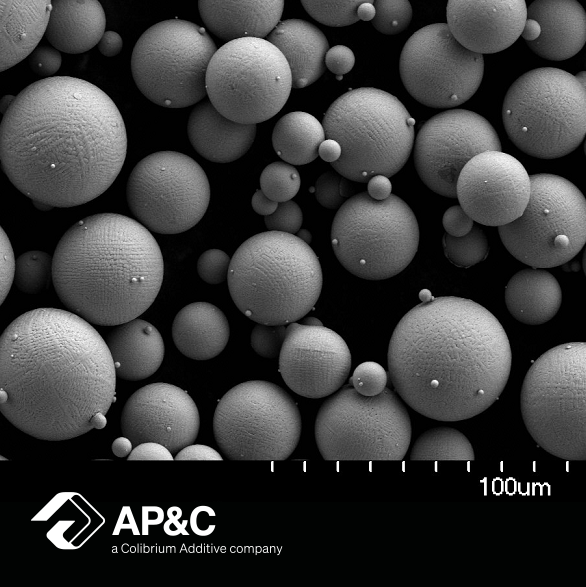
15-45µm
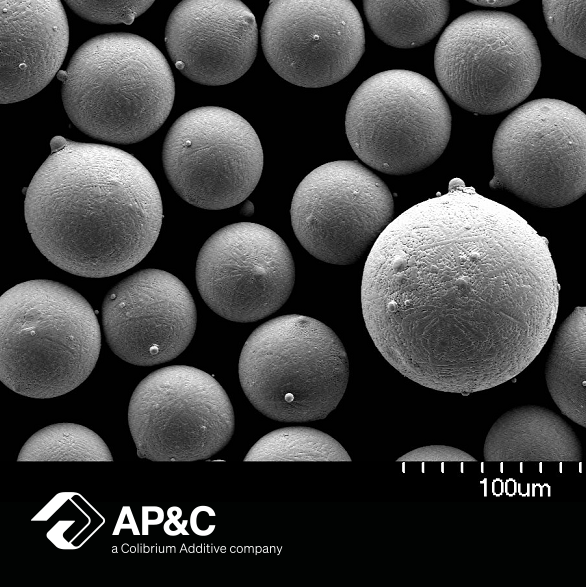
45-106µm
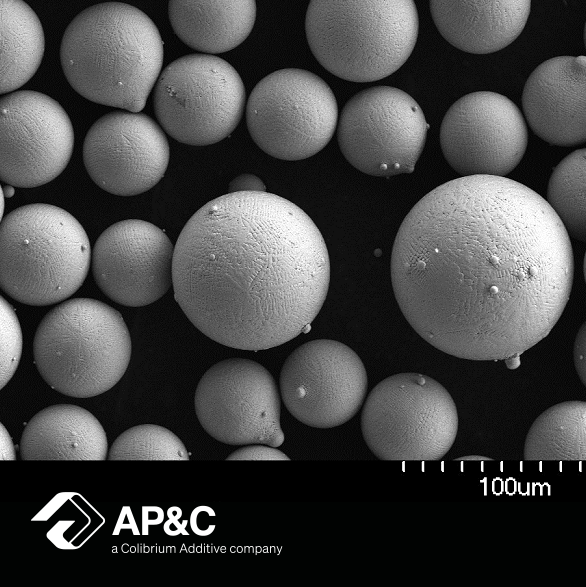
45-150µm
Typical values
PSD
Size distribution by laser diffraction (ASTM B822)
Apparent density (ASTM B212)
Flow rate (ASTM B213)
Application Technology
D10
D50
D90
15-45 µm
22 µm
34 µm
46 µm
4.67
g/cm 3
g/cm 3
13 s
L-PBF
15-53 µm
23 µm
37 µm
51 µm
4.68
g/cm 3
g/cm 3
13 s
L-PBF
45-106 µm
50 µm
67 µm
100 µm
4.75
g/cm 3
g/cm 3
14 s
EB-PBF, L-PBF, DED
45-150 µm
53 µm
90 µm
145 µm
4.79
g/cm 3
g/cm 3
13 s
EB-PBF, L-PBF, DED
Various particle sizes are available upon request.
AP&C’s spherical Nickel Alloy 718 powders possess the ideal characteristics for various powder metallurgy technologies, include Additive Manufacturing. The powders are produced using the patented APATM Plasma Atomization process, which was designed specifically for atomization of high-temperature metals, such as Nickel alloys. With a large industrial capacity for Nickel Alloys powder production, AP&C can support high-volume industrial applications.
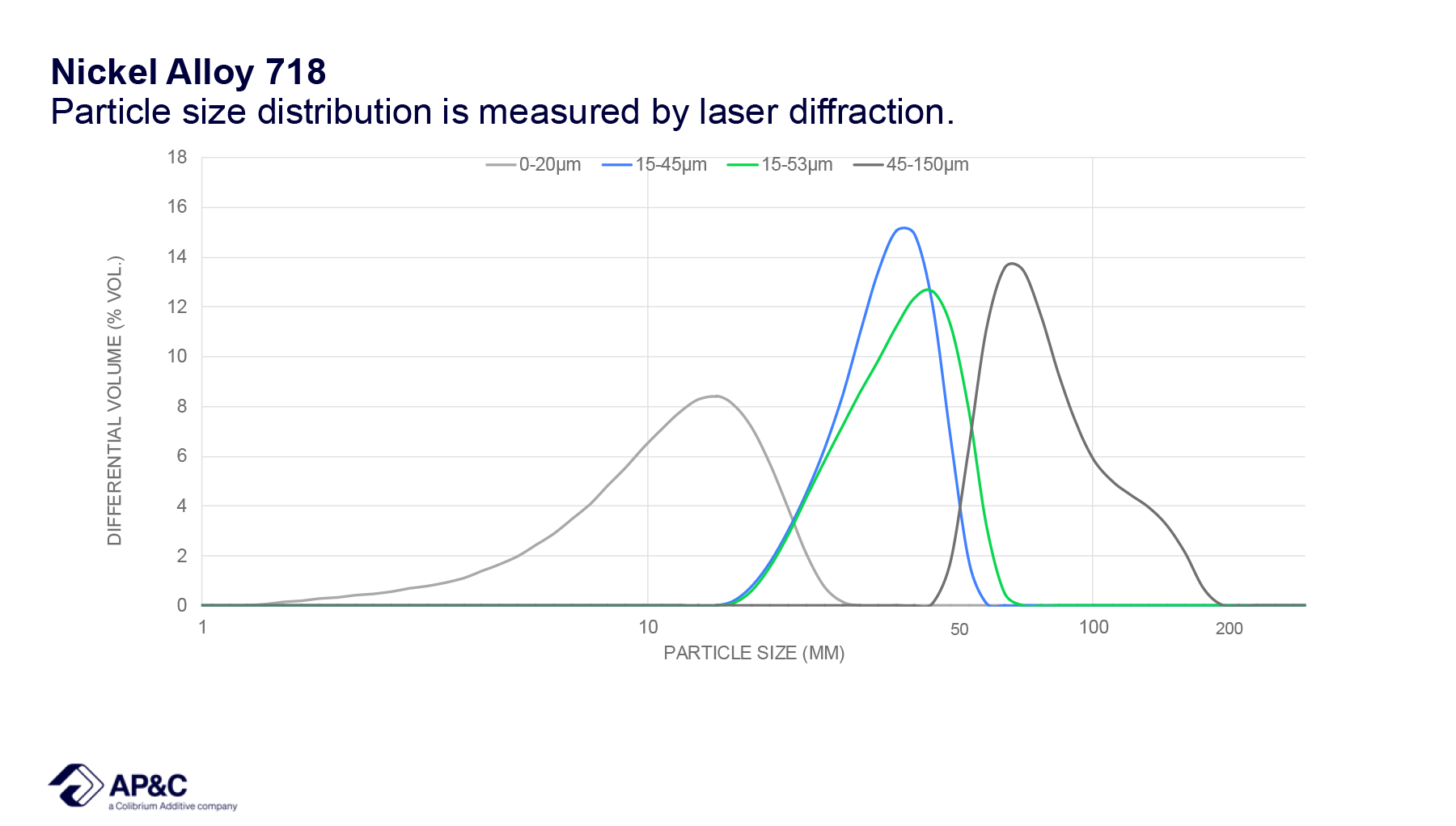
After atomization, the powder is sieved according to customer specifications.
Since 2006, experienced users of Additive Manufacturing, MIM, PM-HIP, Binder Jet, and Coating technologies have trusted AP&C’s powders, which are manufactured using the proprietary APATM Plasma Atomization process. These highly spherical powders contain virtually no entrapped porosities. Additionally, they possess minimal satellite content, resulting in exceptional flowability and packing density.
Metallographic images
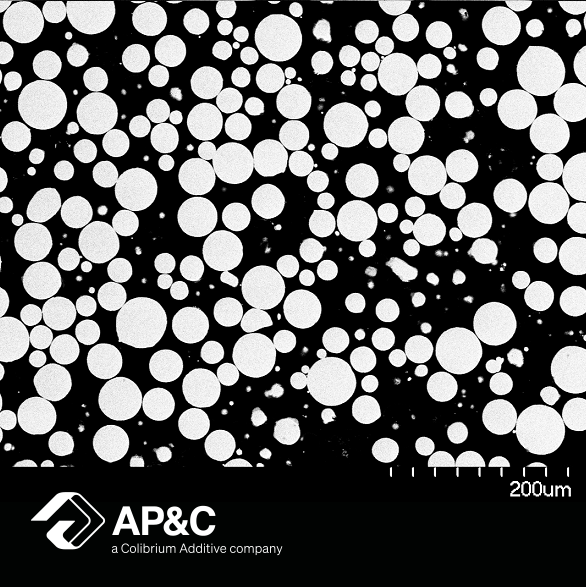
15-45µm
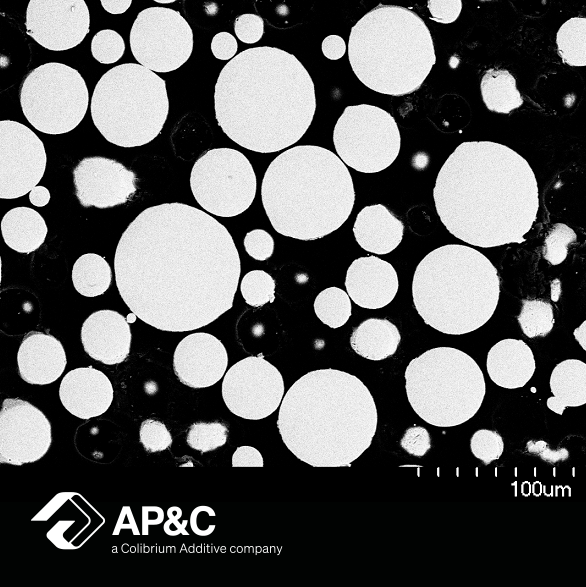
20-63µm
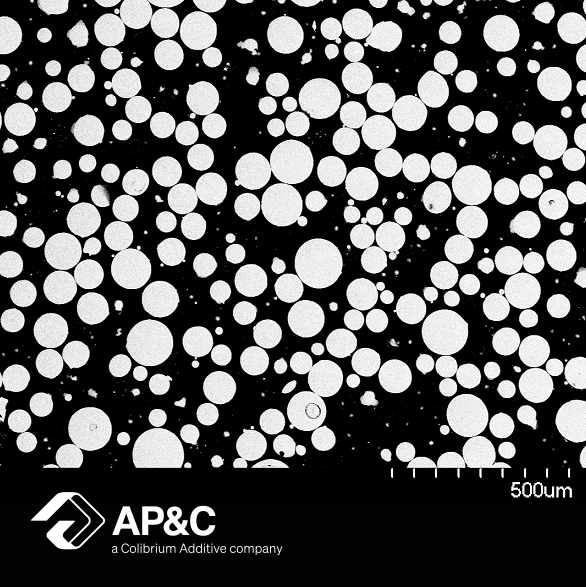